除以苯为原料和C4烃为原料两条路线外,用萘或二甲苯生产邻苯二甲酸酐时也副产顺酐,生产每吨邻苯二甲酸酐大约可回收50kg的纯顺酐。下面
顺酐生产厂家来讲讲更多事项。
In addition to the two routes of using benzene as the raw material and C4 hydrocarbon as the raw material, the production of phthalic anhydride from naphthalene or xylene also produces maleic anhydride as a byproduct. Approximately 50kg of pure maleic anhydride can be recovered per ton of phthalic anhydride produced. Let's talk more about maleic anhydride manufacturers.
苯氧化法
Benzene oxidation method
苯氧化为顺酐是在催化剂存在下进行的。常用催化剂的活性组分均为钒的氧化物(见金属氧化物催化剂),为抑制苯被完全氧化,常加入钼、磷、钛、钨、银及碱金属等元素的氧化物为添加剂,并采用低比表面的惰性物质为催化剂载体,如α-氧化铝、刚玉等。
The oxidation of benzene to maleic anhydride occurs in the presence of a catalyst. The active components of commonly used catalysts are vanadium oxides (see metal oxide catalysts). To suppress the complete oxidation of benzene, oxides of elements such as molybdenum, phosphorus, titanium, tungsten, silver, and alkali metals are often added as additives, and inert substances with low specific surface area are used as catalyst carriers, such as α- Aluminum oxide, corundum, etc.
反应在常压下进行,温度350~400℃。工艺过程由苯的氧化,顺酐的分离和提纯两大部分组成(见图)。苯蒸气和空气能形成爆炸混合物,所以进入反应器的混合气中,苯的浓度应在爆炸极限之外,一般为1%~1.4%(摩尔)。
The reaction takes place under atmospheric pressure at a temperature of 350-400 ℃. The process consists of two main components: oxidation of benzene, separation and purification of maleic anhydride (see figure). Benzene vapor and air can form explosive mixtures, so the concentration of benzene in the mixed gas entering the reactor should be outside the explosion limit, usually 1% to 1.4% (mol).
苯氧化为强放热反应,工业上常采用列管式固定床反应器,有很大的传热面,管外为冷却系统,反应热可用于产生高压蒸汽。离开反应器的气体中含顺酐约1%(摩尔),用冷却的办法可将其中所含一半左右的顺酐冷凝为液体,其余部分则用吸收法回收。
Benzene oxidation is a strong exothermic reaction. Tubular fixed bed reactors are often used in industry. They have a large heat transfer surface. Outside the tubes, there is a cooling system. The reaction heat can be used to generate high-pressure steam. The gas leaving the reactor contains about 1% (mole) of maleic anhydride. About half of the maleic anhydride can be condensed into a liquid by cooling, and the rest can be recovered by absorption.
吸收剂用水或惰性有机溶剂,大多数工厂采用的是水。所得到的吸收液是顺丁烯二酸的水溶液,浓度35%~40%(质量),需用共沸溶剂(例如二甲苯、苯甲醚)进行脱水,把酸重新转化成酸酐。脱水也可在膜式蒸发器中进行。粗酐经减压精馏可得成品。以苯计算,整个过程的顺酐收率为92%~96%(质量)。
Absorbent water or inert organic solvents, most factories use water. The obtained absorption solution is an aqueous solution of maleic acid, with a concentration of 35-40% (mass). It needs to be dehydrated using an azeotropic solvent (such as xylene, anisole) to convert the acid back into anhydride. Dehydration can also be carried out in membrane evaporators. Crude anhydride can be obtained by vacuum distillation to obtain finished products. Calculated with benzene, the yield of maleic anhydride in the entire process is 92% to 96% by mass.
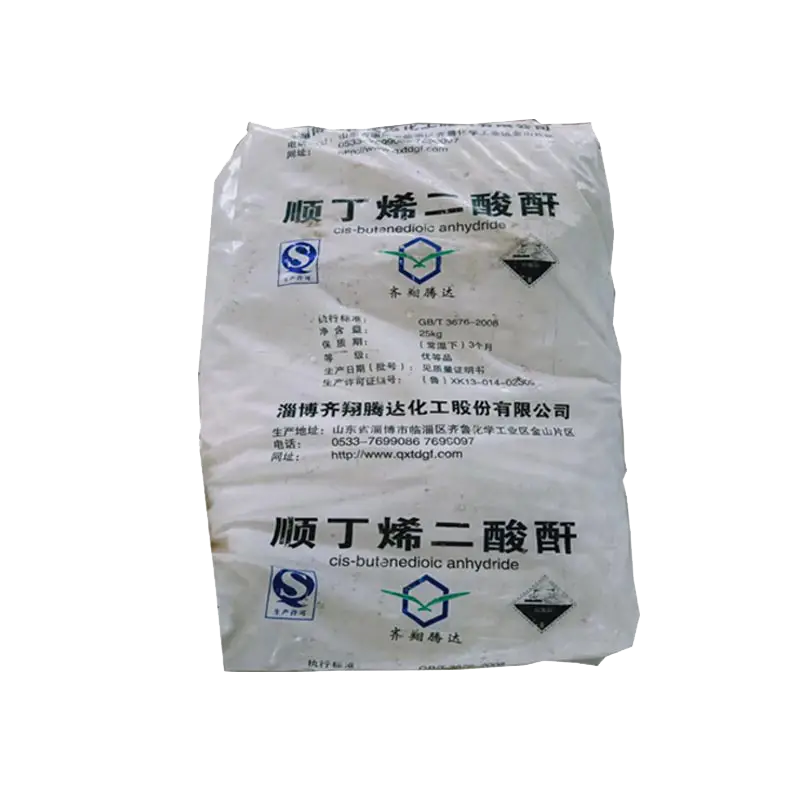
C4烃氧化法
C4 hydrocarbon oxidation method
正丁烷与丁烯均含有与顺酐相同的碳原子数,是生产顺酐的理想原料。由于正丁烷较其他原料低廉,用正丁烷更为有利。其流程与苯氧化法基本相同,催化剂为钒-磷-氧体系,添加剂有铁、铅、锌、铜、锑等元素的氧化物。
Both n-butane and butene contain the same number of carbon atoms as maleic anhydride, making them ideal raw materials for producing maleic anhydride. Due to the lower price of n-butane compared to other raw materials, using n-butane is more advantageous. The process is basically the same as the benzene oxidation method, with a vanadium phosphorus oxygen system as the catalyst and oxides of elements such as iron, lead, zinc, copper, and antimony as additives.
可用固定床反应器或用流化床反应器,反应温度约400℃。正丁烷-空气混合物中正丁烷浓度为1.0%~1.6%(摩尔)。整个过程的顺酐收率按正丁烷计约为50%。
A fixed bed reactor or a fluidized bed reactor can be used, with a reaction temperature of about 400 ℃. The concentration of n-butane in the n-butane air mixture ranges from 1.0% to 1.6% (mol). The yield of maleic anhydride in the entire process is approximately 50% based on n-butane.
That's all for explaining the reaction equation of maleic anhydride. I hope it can be helpful to you. For more information, please come to our website http://www.jnjhhg.cn consulting service